追踪型步进电机驱动板的技术内核
与普通步进电机驱动板相比,追踪目标位置的驱动板需额外满足 “动态响应速度” 与 “定位精度稳定性” 两大核心需求,其技术架构包含三个关键模块:
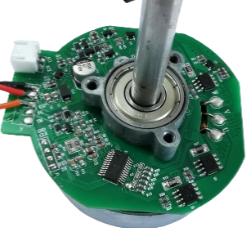
1. 脉冲信号处理与细分控制
驱动板的核心功能是将上位机(如 PLC、单片机)发送的脉冲信号转化为电机的角位移。为实现微米级追踪精度,无刷马达驱动板普遍采用 “电流细分技术”:通过将传统的全步驱动(每步 1.8°)细分为 16 细分、32 细分甚至 256 细分,使电机每步转动角度降至 0.007° 以下。
例如,在安防摄像头追踪系统中,当目标从画面左侧移动到右侧时,上位机发送 1000 个脉冲信号,32 细分驱动板可控制电机转动 1000×(1.8°/32)=56.25°,配合减速齿轮组可实现摄像头 0.1° 的转向精度,确保目标始终处于画面中心。同时,驱动板内置的脉冲平滑滤波电路可消除高频干扰,避免因信号抖动导致的 “丢步” 或 “错步”。
2. 实时位置反馈与闭环控制
单纯的开环控制(仅依赖脉冲数量推算位置)难以应对负载变化导致的定位偏差。追踪型驱动板通过集成编码器(如光电编码器、磁编码器)构建闭环系统:编码器实时检测电机实际转动角度,并将数据反馈至驱动板的 MCU,形成 “指令位置 - 实际位置” 的动态比对。
当偏差超过阈值(如 0.05°)时,MCU 立即调整输出脉冲频率与电流大小,实现 “动态修正”。在天文望远镜追踪星体时,地球自转导致目标每小时偏移 15°,闭环驱动板可通过每秒 100 次的位置比对,将跟踪误差控制在 3 角秒以内,确保星体始终处于观测视野中心。
3. 动态负载适应电路
追踪目标过程中,电机负载可能因外界阻力变化而波动(如机械臂抓取不同重量物体、摄像头遭遇强风扰动)。驱动板的 “自适应电流调节” 电路可实时监测电机绕组电流,当负载增大时自动提升输出电流(最高可达额定值的 1.5 倍),确保扭矩充足;负载减小时则降低电流,减少发热与能量损耗。
例如,在太阳能板追日系统中,驱动板在清晨推动 panels 转动时(负载小)电流为 1A,正午对抗强风时电流自动升至 1.5A,既保证追踪精度,又避免电机过热。
追踪场景下的性能优势
追踪目标位置的步进电机驱动板的性能优势,直接体现在复杂环境下的 “精准度” 与 “可靠性” 上,具体表现为三个维度:
1. 零丢步设计,确保轨迹连续性
在高速追踪场景中(如无人机追踪移动车辆),电机转速可达 3000rpm,传统驱动板可能因脉冲频率过高导致 “丢步”(电机实际转动角度小于指令角度)。而追踪型驱动板通过三项技术避免这一问题:
- 采用高速光耦隔离(响应速度>1MHz),确保高频脉冲信号无衰减传输;
- 内置 “扭矩预加载” 算法,提前提升绕组电流,防止启动瞬间因惯性导致的丢步;
- 实时监测电机反电动势,当检测到 “堵转前兆” 时自动降低转速,待负载稳定后再加速追赶。
2. 宽速域自适应,兼顾高速与低速性能
目标追踪往往涉及 “快速移动 - 精准停靠” 的动态过程,驱动板需在宽转速范围内保持稳定性能。例如,在 3D 打印机的轮廓追踪中,打印直线时电机需高速运转(1000rpm),打印拐角时需骤降至 100rpm。驱动板通过 “S 型加减速曲线” 控制:转速变化时先缓慢加速,达到设定值后匀速运行,减速时逐渐降低速度,避免因惯性导致的定位超调。
这种设计使电机在 0-3000rpm 范围内的转速波动控制在 ±2rpm 以内,确保追踪轨迹的平滑性。
3. 多模式通讯,适配复杂控制系统
不同追踪系统的指令传输方式差异较大,驱动板需支持多种通讯协议:
-
脉冲 + 方向模式:通过脉冲数量控制位移,方向信号控制转动方向,适用于简单的 PLC 控制系统;
-
串口通讯(RS485/Modbus):支持上位机发送 “目标位置” 指令(如 “转动至 35.5°”),驱动板自主计算脉冲数量,适用于远程监控系统;
-
以太网 / 无线通讯:集成 WiFi 或以太网模块,可直接接入物联网平台,适用于分布式追踪网络(如农业大棚的多区域温湿度传感器追踪)。
实战场景:从实验室到产业一线
追踪目标位置的步进电机驱动板的技术优势,在各领域的实战应用中得到充分验证:
1. 天文观测:星体追踪系统
大型天文望远镜需要 24 小时追踪星体的周日运动(因地球自转而产生的天体视运动)。驱动板通过接收 GPS 模块的时间信号与天文算法生成的方位角指令,控制赤经、赤纬轴电机以 0.001°/s 的精度转动。256 细分技术配合 17 位编码器反馈,使望远镜的定位误差控制在 1 角秒以内,确保长时间曝光拍摄时星体始终处于视场中心。
2. 工业视觉:动态工件检测
在流水线产品质检中,高速移动的工件(如手机屏幕)需要视觉系统实时追踪并拍摄缺陷。驱动板接收视觉传感器的位置信号后,控制镜头平移电机在 50ms 内完成从 “待机位” 到 “检测位” 的移动,同时通过 16 细分控制确保镜头对焦精度 ±0.01mm,避免因工件移动导致的模糊成像。
3. 安防监控:智能目标锁定
具备自动追踪功能的安防摄像头中,驱动板通过分析画面的运动目标(如行人、车辆),计算出目标在图像中的坐标偏移量,转化为水平 / 垂直方向的电机转动指令。32 细分驱动使摄像头转向精度达 0.1°,配合 “预判算法”(根据目标移动速度提前调整转向),可实现对时速 30km/h 以内目标的持续锁定。
选型与优化指南
选择追踪目标位置的步进电机驱动板时,需结合应用场景的三大核心参数:
1. 精度需求:细分倍数与编码器分辨率
- 微米级定位(如 3D 打印):选择 256 细分 + 17 位编码器的驱动板;
- 毫米级定位(如安防监控):16 细分 + 14 位编码器即可满足需求;
- 成本敏感场景(如玩具追踪):4 细分 + 开环控制可降低成本。
2. 动态性能:最高脉冲频率与加减速曲线
- 高速追踪(如流水线检测):选择最高脉冲频率≥200kHz 的驱动板,支持 S 型加减速;
- 低速平稳追踪(如天文观测):优先考虑低频振动小的驱动板,可选择 “正弦波电流驱动” 模式。
3. 环境适应性
- 户外场景(如太阳能追日):选择 IP65 防护等级、宽温范围(-40℃~85℃)的驱动板;
- 工业强干扰环境:需具备光电隔离(隔离电压≥2500V)与浪涌保护功能。
随着自动驾驶、机器人导航等领域对 “动态追踪精度” 的要求不断提升,步进电机驱动板正朝着 “更高细分倍数”“更快响应速度”“更智能的自适应算法” 方向演进。未来,结合 AI 预测算法的驱动板将能提前预判目标运动轨迹,实现 “未动先转” 的前瞻式追踪,进一步突破现有定位技术的边界。
-
IS09 磁性编码器方案
在工业自动化、机器人技术、伺服驱动等对精度、可靠性和环境适应性要求极高的领域,精准的位置和速度反馈是实现高性能控制的关键。IS09 磁性编码器方案,作为先进的非接触式位置检测解决方案,凭借其独特的技术优势和卓越的工业级表现,正日益成为工程师信赖的核心传感部件。¥ 0.00立即购买
-
MT6501在线编程角度位置磁编码IC
在工业自动化、机器人关节、无人机云台等对角度位置检测要求严苛的应用场景中,MT6501作为一款集高精度、强抗扰性、灵活编程能力于一身的磁旋转编码器芯片,正成为工程师优化系统设计的理想选择。其独特的在线编程(In-System Programming, ISP)功能,彻底改变了传统磁编码器的配置与校准流程,为复杂环境下的位置感知带来前所未有的便捷与精准度¥ 0.00立即购买
-
智能低压水泵无刷电机驱动板方案
高效节能、智能控制的水泵驱动解决方案——智能低压水泵无刷电机驱动板是一款专为低压直流无刷水泵(DC Brushless Pump)设计的高集成度电子驱动控制器。该产品采用先进的无感FOC(磁场定向控制)算法与自适应PID控制技术,支持宽电压输入(12V-48V DC),适用于太阳能水泵、车载水循环系统、农业灌溉、小型工业冷却等场景,具备高效率、低噪声、长寿命和智能化管理等核心优势。¥ 0.00立即购买
-
闭环步进电机驱动板方案
在现代工业自动化、精密仪器和高端装备领域,对运动控制的精度、效率和可靠性要求日益严苛。闭环步进电机驱动板技术应运而生,它融合了传统步进电机的简易性和伺服系统的闭环精度,成为解决步进电机“失步”痛点、提升系统性能的关键技术。以下将从核心原理、系统架构、核心优势、应用场景及选型要素等方面进行层次化阐述。¥ 0.00立即购买
-
云台无刷马达驱动板方案
云台BLDC驱动方案——高精度、低延迟、多场景运动控制核心¥ 0.00立即购买
-
风扇无刷电机驱动(板)方案
随着人们对电吹风的需求和要求不断增加,其能耗、噪音和风速等参数是考核产品最直接的标准。电机就是最电吹风重要的元件之一。为了满足人们在不同的使用场景和不同的使用环境,需要可调速范围广,噪音低、使用寿命长的电机。根据不同使用场景还需要有不同的模式。为了解决传统的交流电机无法满足用户节能、舒适要求的问题,艾毕胜电子充分发挥技术力量雄厚的优势,结合以往研发经验,开发出风扇无刷电机驱动解决方案。¥ 0.00立即购买